When the time came to convert and retrofit a cage-type stranding machine, cable manufacturer Lapp chose the all-in-one service package from EUCHNER Safety Services. The machinery safety specialist completed the entire conformity assessment process, including all required design and conversion work. The final CE marking signed by EUCHNER Safety Services verifies the overall production facility’s compliance with all health and safety protection requirements contained in Machinery Directive 2006/42/EC.
Located behind a pair of roller gates with windows, the cage-type stranding machine rotates at a constant speed around its horizontal axis. It is surrounded by several drums on coil carriers. A motorized twin-wheel capstan pulls bundled conductors out of the stranding machine’s safety zone. The multi-conductor cable passes through a banding station and is then stranded and wrapped before being wound onto the take-up drum. Lapp’s production facility manufactures special cables containing up to 24 conductors each, which are used mainly as servo cables for drives. Once all doors are closed, the manufacturing process runs almost fully automatically. Built in 1991, the machine was recently upgraded to meet the latest electromechanical, control and safety engineering standards, and it now bears a current CE marking.
In keeping pace with technological progress, the reliable cage-type stranding machine has undergone periodic electrical, control and safety engineering updates over the years. Wearing parts were replaced and converters were changed. Last year, Lapp decided to give the special machine an integrated, long-term retrofit.
Lapp, a family-operated business founded in Stuttgart in 1959, has made a name for itself worldwide as a supplier of integrated cable and connection technology solutions. Its range of products includes standard and highly flexible cables, industrial plug connectors and screw fastening equipment, custom assembly solutions, automation equipment and robotics solutions for the smart factory of tomorrow.
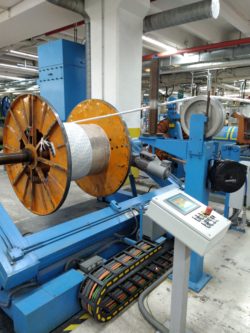
Take-up drum
Retrofitting is an economical alternative to purchasing a new machine whenever the underlying hardware and mechanical components are robust and sound. This also applies to sustainability and downtimes. Continuing to use an essentially intact machine protects natural resources. “Many projects have demonstrated that professionally retrofitting an aging machine can put it on a par with a new one in terms of costs and availability,” says Detlef Ullrich, Head of Safety Services at EUCHNER. Once the measures are complete, the overhauled machines can usually continue operating in the production process for many years to come.“Although we weren’t under any formal obligation to do this, we thought the right approach would be to hand over the whole conformity assessment process, including all of the implementation work and the final CE marking step, to a single source,” says Markus Pressel, who is responsible for process development and machine technology at Lapp.
The safety design was one of the main areas addressed alongside the electrical engineering and control aspects. The stranding machine had always been safe, but our concept of safety in 2021 is smarter, more versatile, easier to use and maintain and more secure against tampering. The regulated documentation process involved in the conformity assessment process is demanding and calls for great technical expertise and in-depth knowledge of the applicable standards. Pressel and his team thought performing this work in house would take too long, particularly since the production facility for special cables should not be down for an extended period.
The quotation from EUCHNER Safety Services was the most convincing bid submitted to Lapp: “Clearly and understandably structured, with transparent costs,” remembers Pressel. The all-in-one package included the service modules for the entire conformity assessment process with risk assessment and safety design, verification of the safety functions, validation of the overall installation and the signing of the declaration of conformity.
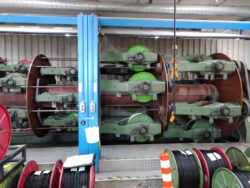
Cage-type stranding machine
One of the decisive factors in favor of EUCHNER Safety Services was that the full-service provider offered to perform all of the conversion work, including documentation, the safety design, the mechanical equipment, the electrical design and the fluid and control cabinet design. Its scope of services additionally included carrying out all assembly, installation and setup work, plus all testing and the final acceptance, in compliance with the relevant directives 2006/42/EC (Machinery Directive), 2014/35/EU (Low-Voltage Directive), 2014/30/EU (EMC Directive) and particularly the DIN EN ISO 13849-1 standard.
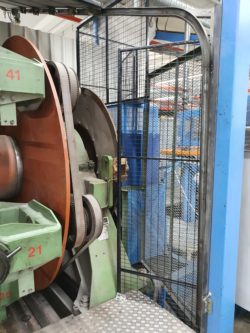
Cage-type stranding machine drive
“On our first customer visit, we familiarize ourselves with the machine, collect data, record any mechanical defects and analyze potential hazards as the basis for our risk assessment and the safety design,” says Perica Lekavski, Project Manager at EUCHNER Safety Services, describing the procedure. On the subsequent visit to the site, Lekavski presented the risk assessment and the safety design for the installation. The plan was to install a modern safety PLC to bring the cage-type stranding machine into line with modern safety engineering requirements. In agreement with the customer, EUCHNER Safety Services developed detailed plans for the hardware, fluid and mechanical design, for software programming, for verification of the safety functions and for preparing the validation documentation. “We worked together professionally as equal partners. What’s more, the team from EUCHNER quickly familiarized itself with the special requirements in the cable industry,” emphasizes Pressel.
In addition to replacing various wearing parts, EUCHNER Safety Services modified the circuit structure in accordance with the results from the risk assessment (analysis of the hazard locations). The take-up drum was given a new protective enclosure with door locking mechanisms and control panels for manual operation. Additional protective plates were mounted on the stranding cage, twin-wheel capstan and unwinder to minimize the risk of injury. The expanded Safe Limited Speed (SLS) safety function and the selection of operating mode now also permit safe inching mode when the guard is open. Implementing all measures significantly enhanced both safety and convenience when operating the installation. The cage-type stranding machine now meets all requirements from the applicable standards.
Lapp had estimated 14 days of downtime for the conversion measures. EUCHNER Safety Services completed all conversion work, including setup, in ten working days, returning the installation to production sooner than planned. The CE mark on the cage-type stranding machine and the declaration of conformity EUCHNER Safety Services was authorized to sign stand for safety at the highest level. “EUCHNER Safety Services definitely set standards with this pilot project, and we would gladly hire them again for comparable tasks in the future,” summarizes Pressel.