ESM-CB-AZ-FI2-BR-IO-158875 (Order no. 158875)
IO-Link Gateway with relay outputs for BP/BR switches
- IO-Link device for reading process and device data of BP/BR safety switches and transferring them to a higher-level control system
- Control of guard locking of BP/BR switches, depending on the switch used
- Compact version measuring only 18 mm in width
- Rail mounting
- LED status indicators
- Sensor circuit 1: connection of single- or dual-channel safety switches with floating contacts; short circuit, earth fault and ground fault detection
- Sensor circuit 2: connection of 2 safety outputs for BP/BR switches
- Use as safety relay with two safe outputs
- Start button and feedback loop can be connected
- Safety relay: use up to category 4 according to EN ISO 13849-1
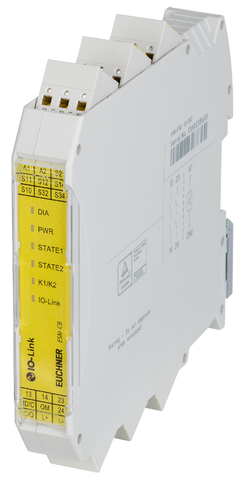
Description
Connection options
The following functions are possible given the corresponding wiring:
- Start input for automatic start or a monitored start button
- Monitoring of downstream relays or contactors (feedback loop)
- Short circuit monitoring to detect short circuits between the connecting cables and to shut down the outputs or prevent relay starting if necessary
- Earth fault/ground fault monitoring to detect short circuits between the connecting cables and earth or ground and to shut down the outputs or prevent relay starting if necessary.
Relay outputs
- The outputs are redundantly designed and electrically decoupled.
- Simultaneity monitoring of the safety outputs to monitor safety components over time.
- No time-delayed shutdown
Industry 4.0 ready
Process data are cyclically sent to the control system via IO-Link. These data include all status signals, such as the door or guard locking position, and the indication of whether a switch is in the limit range of the actuating range.
The process data are available to the control system after approx. 200 ms and can be used for the automation process.
Moreover, acyclical polling can be used to collect environmental data such as the internal switch temperature, the applied voltage or the ID of the transponder used, as well as other values.
Plug and Play series connection
- Connection for safety switches with BR technology without addressing the individual switches
- The wiring and configuration work is minimized.
Device data and events
The higher-level control system can poll more than 30 different items of information from the connected switches. Comprehensive data transmission via IO-Link enables targeted preventive maintenance, for example.
Simple implementation of innovative applications
Device data from the actuators used can be employed to detect individual rotary table positions or different containers, for example.
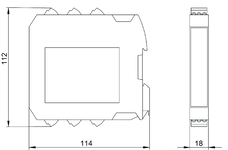
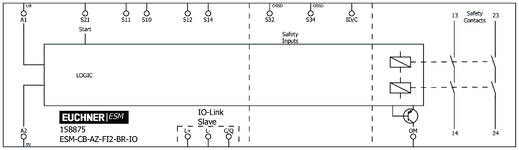
Dimensional drawings

Connection examples
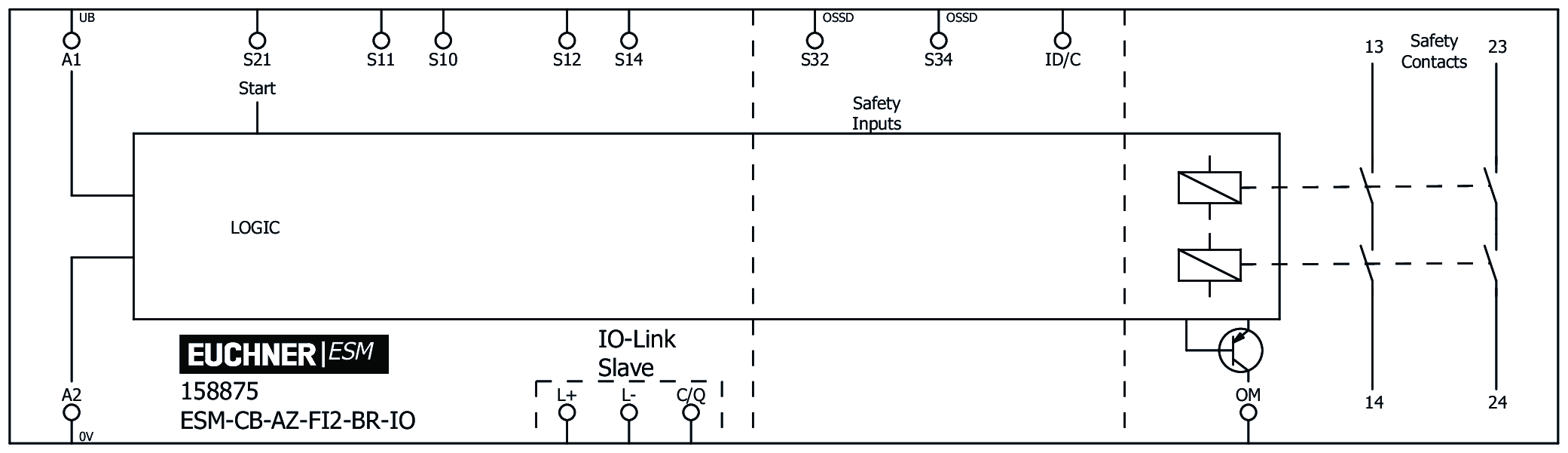
Technical data
Approvals
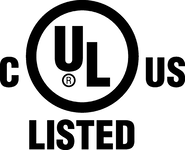
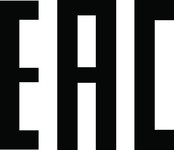
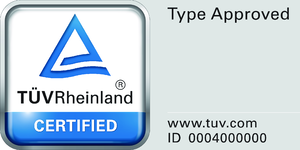
Operating and display elements
LED display | 1x operating voltage display PWR, 5x status displays DIA, STATE1, STATE2, K1/K2, IO-Link |
Electrical connection values
Power consumption | |
at 24 V DC | 1.44 W |
Connection cross section | 0.2 ... 1.5 mm² |
Rated insulation voltage Ui | 320 V |
Rated impulse voltage Uimp | |
Leakage path/air gaps | 4 kV |
Duty cycle | 100 % |
Overvoltage category according to IEC EN 60664-1 | 2 |
Power dissipation | max. 6.45 W ((US=30 V, UL=30 V, I²=72 A²)) |
Degree of contamination (external, according to EN 60947-1) | 2 |
Mechanical values and environment
Stripping length | 8 mm |
Dimensions | 17.5 x 116.5 x 114.5 |
Connection type | plug-in spring terminals |
Type specification | Electromechanical relay with positively driven contacts according to IEC/EN 61810-3 (EN 50205) |
Installation orientation | vertical or horizontal |
Storage temperature | -25 ... 70 °C |
Atmospheric humidity | max. 75 % rH |
Mounting type | Mounting rail TH 35 (EN IEC 60715) |
Degree of protection | |
IP20 | |
IP54 (Installation location, min.) | |
Ambient temperature | |
(operation) | -25 ... 60 °C |
Material | |
Housing | PBT, gray |
Contact | AgSnO2 |
permissible shock and vibration load | 10 Hz...150 Hz, 2 g |
Characteristic values according to EN ISO 13849-1 and EN IEC 62061
Mission time | 20 y (This value is dependent on the number of switching cycles and the switching current.) |
Category | |
according to EN ISO 13849 | 4 |
Performance Level | |
according to EN ISO 13849 | (A demand rate of the safety function of once per month is required for applications in PL e.) |
PFHD | |
for IEC 61508 – high demand | 1.00 x 10-9 (This value is dependent on the number of switching cycles and the switching current.) |
SIL CL | 3 |
Miscellaneous
ESPE type | Typ A |
Downloads
Complete package
Download all important documents with a single click.
Content:
- The operating instructions and any additions to the operating instructions or brief instructions
- Any data sheets to supplement the operating instructions
- The declaration of conformity
Single Documents






Other Documents

Homologation
Homologación
EAC
Homologação
Omologazione
认证
認可
승인
Сертификат
Atest
Engedély
Разрешително
Godkendelse
Heakskiit
Hyväksyntä
Έγκριση
Odobrenje
Atļauja
Patvirtinimas
Goedkeuring
Godkjenning
Dopuszczenie
Godkännande
Dovoljenje
Povolenie
Onay
Дозвіл

Homologation
Homologación
c_UL_us_E93776_ESM-CB
Homologação
Omologazione
认证
認可
승인
Сертификат
Atest
Engedély
Разрешително
Godkendelse
Heakskiit
Hyväksyntä
Έγκριση
Odobrenje
Atļauja
Patvirtinimas
Goedkeuring
Godkjenning
Dopuszczenie
Godkännande
Dovoljenje
Povolenie
Onay
Дозвіл


Ordering data
Ordernumber | 158875 |
Item designation | ESM-CB-AZ-FI2-BR-IO-158875 |
Gross weight | 0,231kg |
Customs tariff number | 85371098 |
ECLASS | 27-24-26-07 Field bus, decentralized peripheral - basic device |